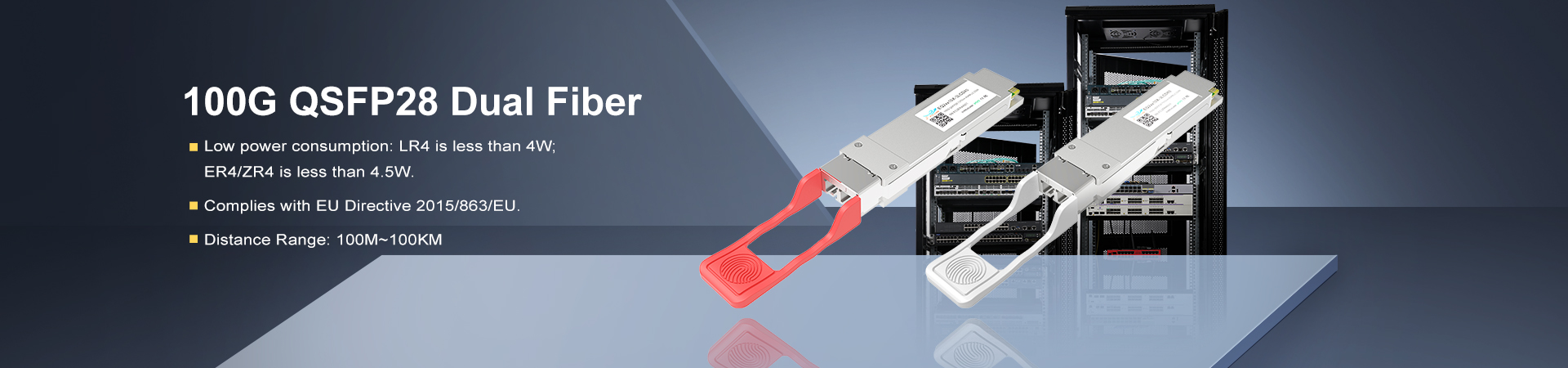
High speed cable production process
High speed cable DAC is used for the connection of short distance network devices, such as server, switches,storage and so on. It is a low cost measure of network devices connection. So far there are common DAC cables including 10G SFP+ to 10G SFP+ DAC cable, 25G SFP28 to 25G SFP28 DAC cable, 40G QSFP+ to 40G QSFP+ DAC cable, 40G QSFP+ to 4x SFP+ DAC cable, 100G to 100G QSFP28 DAC cable, 100G to 4xSFP28 DAC cable. Next we, ETU-LINK, will take you to know the production procedure of DAC high speed cables.
The production of high speed DAC cables includes 6 steps. The first step is the extrusion of insulated core wire. It is the base of cable production. A cable’s quality play an important role in the follow-up procedures. The second step is parallel winding. This procedure has great importance to the performance of cables, including impedance, delay difference, attenuation. So, it has to be serious to follow the requirements of craft to produce, and to test the electrical performance. This is to make sure that wrapped core wire meet the requirements.
The third step is parallel cabling. The cabling process affects the overall performance of the cable. Therefore, in the production process, it is necessary to strictly control the consistency of each wrapped core wire, and test the electrical properties such as impedance, delay difference and attenuation, so as to ensure that the cabling core wire meets the requirements.
The fourth step is wire braiding, which needs to control the tension and arrangement of the wire, otherwise it will affect the overall performance of the wire in the braiding process.
The fifth step is to push out the outer cover of the wire rod. The outer cover is to put a layer of polyolefin material on the outside of the braided or cabled wire rod through the push out machine. The tightness of the outer cover will also affect the appearance of the wire rod and the processing of the finished products of customers. Therefore, it is necessary to control the tension, wire arrangement and push out mode.
After completing the above steps, the last step is to complete the electrical performance test. The test items mainly include impedance, attenuation, delay difference, etc. Finally, judge whether the wire meets the standard according to the data.
Categories
New Blog
Tags
© Copyright: 2025 ETU-Link Technology CO ., LTD All Rights Reserved.
IPv6 network supported
Friendly Links:
易天官网